Bilder: Fraunhofer IIS
Das vollständige Röntgen endmontierter Fahrzeuge lässt sich aktuell nur an wenigen Orten weltweit unter Laborbedingungen realisieren, unter anderem am Entwicklungszentrum Röntgentechnik des Fraunhofer IIS in Fürth. Die Prozedur ist allerdings aufwendig und kostspielig, sodass deren Einsatz gegenwärtig Unternehmen vorbehalten bleibt, die insbesondere sicherheitsrelevante Bauteile im Entwicklungsprozess überprüfen.
Mit dem neu entwickelten AIR-System (Antriebsbatterieinspektion mittels Röntgen) ändert sich das laut den Forschern. Sie erklären: „Das System ermöglicht es, die mechanische Integrität von Batteriemodulen visuell zu bewerten, indem ein Röntgenbild des Fahrzeugs und der im Unterboden montierten Antriebsbatterie aufgenommen wird. Hierfür wird das Fahrzeug in das Messsystem hineingefahren – der Messaufbau erinnert an eine klassische Waschanlage. Die Röntgenaufnahmen werden aus der Vogelperspektive erstellt. Die über dem Fahrzeug positionierte Röntgenquelle emittiert einen feinen Röntgenstrahl, der das Fahrzeug einschließlich der Batterie passiert und von einem am Boden positionierten Detektor aufgefangen und verarbeitet wird.“
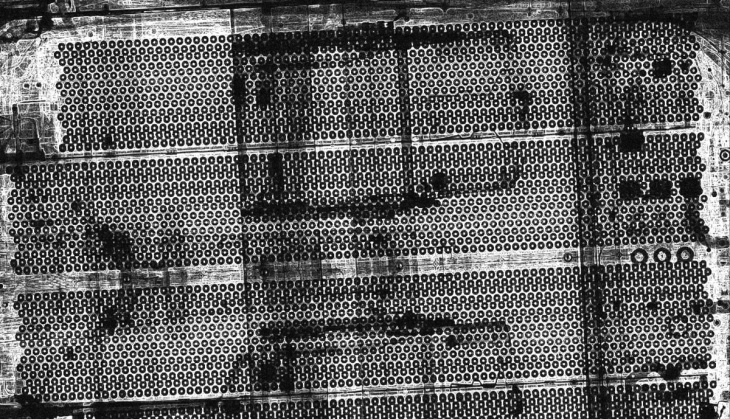
Scan eines E-Auto-Batteriemoduls mit AIR
Selbst in voll gekapselten Batteriemodulen sei eine Detailbetrachtung der Batterie möglich, um Aussagen über den mechanischen Zustand einzelner Batteriezellen, des Batterierahmens und weiterer Merkmale treffen zu können. Das neue System sei dabei speziell auf die Anforderungen einer möglichst schnellen und kostengünstigen Prüfung ausgelegt.
Einerseits seien solch strikte Sicherheitsvorkehrungen gegenwärtig unumgänglich, um die Betriebssicherheit der Fahrzeuge – und damit auch die Sicherheit der Insassen und anderer Verkehrsteilnehmer – gewährleisten zu können. Andererseits sei es unter Gesichtspunkten der Nachhaltigkeit und Ressourcensparsamkeit fragwürdig, unbedenkliche, funktionsfähige Batterien zu recyclen. „Hier gibt es einen großen Bedarf des Marktes nach einer zusätzlichen objektiven Bewertungsmöglichkeit von Fahrzeugbatterien. Deshalb forschen wir bereits seit vielen Jahren an Röntgensystemen, die bei der Begutachtung von Hochleistungsakkus eine zentrale Rolle einnehmen könnten“, so Michael Salamon, Gruppenleiter am Entwicklungszentrum Röntgentechnik des Fraunhofer IIS.